Content Attributes
The construction industry is one of the biggest contributors to the world economy and is predicted to experience 35% global growth in the decade to come. Yet, it is plagued by inefficiencies, many of which can be reduced through the use of new construction technologies.
One of the construction industry’s biggest problems, delays, can be mitigated by adopting technologies like construction simulation and optioneering software. Project managers can foresee possible delays and immediately offer alternative solutions by simulating various outcomes.
With construction optioneering software like ALICE Technologies, you can optimize project schedules to stay ahead of possible slowdowns, reduce the project duration, and save on equipment and labor costs.
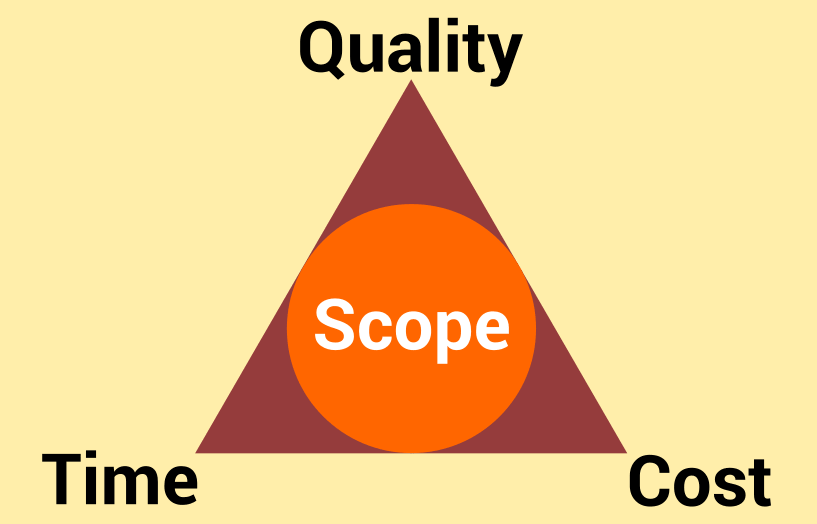
But it’s impossible to tackle construction delays without a firm understanding of what causes these delays in the first place. What are the primary causes of construction delays?
Budgeting problems
Wrong estimation of a project’s budget can hugely affect the progress of a project. The project is delayed in some cases. In other cases, it is completely abandoned, especially if the budget estimate is far from what it should be.
Good estimates ensure that money is always enough for materials, staff wages, labor, project approvals, possible emergencies, and potential inflation in the cost of materials. For instance, in 2019, the cost of construction materials went up by about 10%.
Sometimes, it isn’t even a wrong budget estimation but the inability to monitor how much of the budget has been spent over a certain period of time, especially when the project team is battling inflation.
Inadequate planning
Sometimes, these delays happen because the project was not well planned. The planning process is a very important part of any construction project.
Several professionals need to be involved in the execution of a project. Contractors and project managers have to allocate resources more efficiently and identify tasks or activities that depend on each other. This way, it’s easier to assess risks to better handle issues like shortage in labor and supply more efficiently should they pop up.
But even with proper planning, it’s not easy to predict how the combination of these factors and the use of resources will play out in reality. But it’s possible to do this with construction simulation software in your corner.
With this solution, you can enter all variables that make up the project, and the tool simulates the combination of these resources in real-time, optimizes the plans, and tells you the best way it works. Simulating your plans helps you identify potential delays, some of which you can then work to eliminate.
Amendments in engineering design
A change in the engineering design of a civil engineering edifice can cause a significant delay in construction. This is particularly true of massive construction projects like big buildings, dams, reservoirs, aquariums, etc.
Once there is a change in the design, there must be a corresponding change in the project schedule network diagram for every change in the design. The bill of materials and labor provisions also have to be revisited.
Though these changes in the project schedule are inevitable with a change in engineering design, construction simulation software can help reduce potential delays by reducing the time it takes to draft new project schedules.
Some solutions like ALICE allow you to quickly incorporate changes in the original design, then align your estimates and schedule to conform to the latest design.
Unavailability of good equipment
The unavailability of equipment required for project execution in the project plan will undoubtedly slow down the project. Faulty or bad machines or equipment will have just about the same effect too. Therefore, all machines and such heavy equipment logistics need to be sorted out before the project begins.
Poor weather
Weather is one of the primary causes of construction delays. Sadly, it is beyond anyone’s control. There’s only so much project managers and planners can account for when drawing up their plans.
This is especially true for long-term projects, which experience several seasonal changes. Severe weather may create unsafe conditions for the workers. They may also adversely affect what’s under construction. For instance, rainstorms may wash off the wearing course of a road under construction or make the walls of a drilled pile cave in.
Inefficient material management
Material is a major cost expense in any construction project. Proper material management ensures that the right quality and quantity of material is chosen, transported, and used with minimal wastage.
Poor management of materials can inflate the project’s total cost, sometimes to a level that the project cost then surpasses its budget.
Conclusion
The primary causes of construction delays, as highlighted, are inefficient material management, poor weather, budgeting problems, changes to engineering design, and poor planning.
These delays can be mitigated by tackling the root causes through proper communication, optimization, and simulation of project plans using construction optioneering software and providing leeway in construction schedules to accommodate any changes that could lead to delays.