Content Attributes
Intermediate Bulk Containers (IBCs) are used for the storage and transportation of a range of solids and liquids. They are usually made from industrial-grade plastic and can be either flexible or rigid. They have a cube shape design that allows for easier storage than cylindrical barrels.
IBCs are capable of holding up to 1000 liters of materials and are also available in smaller sizes. They are easy to clean using the IBC reconditioning systems, which makes them economical and reusable for transporters.
IBCs are mainly used in the transportation of raw materials, chemicals, food syrups, granulated food, wine, biological waste, pharmaceutical compounds, paints, rainwater, as well as petrochemical products.
It is very important to ensure that all residue and traces of previous loads are removed before reusing IBCs. Large haulage companies usually have their own on-site IBC reconditioning systems while smaller businesses use IBC reconditioned totes from trusted suppliers.
Intermediate Bulk Containers are a fairly new invention having only been patented in 1993 by Olivier J. L. D’Hollander, a Belgian inventor. There are numerous benefits associated with using them that they are quickly replacing traditional barrels and cans. One of the key advantages is that they are dust tight and prevent leakage and contamination.
Advantages of IBCs
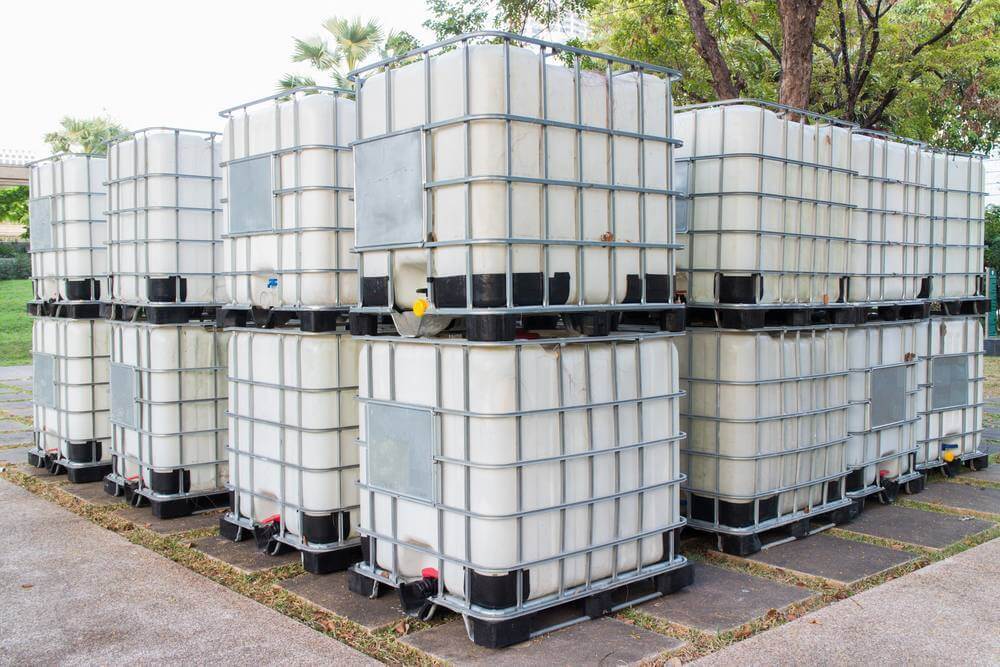
IBCs offer numerous advantages over traditional barrels and other cylindrical transport containers. Here are the top advantages of Intermediate Bulk Containers:
- Efficient Storage: Intermediate Bulk Containers are cube-shaped, which makes it easier to store large quantities due to the tessellating shape.
- Time-Saving: IBCs are easier to load on fork lift trucks and pallet stacks because of their regular shape, which helps save time and effort.
- Reduces Waste: Intermediate Bulk Containers are able to hold a large quantity of product, which reduces the number of containers needed thus reducing wastage.
- Recyclable: IBC reconditioning units allow IBCs to be used numerous times, which is not only good for the environment but also for company budgets.
IBC Reconditioning Systems
IBC reconditioning systems are used to clean the tanks thoroughly and dry them so that they can be reused. Cleaning Intermediate Bulk Containers is done using two automatic systems. The first system is used to wash and rinse the IBCs and the second system dries them.
Automatic Washing System
The automatic IBC washing system first washes, drains, and then rinses used Intermediate Bulk Containers both externally and internally so that they can be reused. The walking beam conveyor system ensures that the IBCs are in the proper position for the washing process to start.
Each system comprises expandable modules to incorporate extra features in the future. The system consists of 2 parts. First, the IBC is drained of its contents followed by the washing process that uses 4 jets of steaming hot water, which ensures that all areas of the tank are cleaned thoroughly and ready for the drying process.
Automatic Drying System
The automated IBC drying system has been designed such that it’s loaded at one end and transfers the Intermediate Bulk Containers between each process system automatically. Pneumatics are used in the transfer system to move the IBC in place. The drying system is then activated once the Intermediate Bulk Containers are firmly in place. The system is controlled by an operator via a control panel facilitating any necessary changes to the processing time.
Hot air is directed into each of the air nozzles through a galvanized steel manifold. The client is responsible for providing the hot air supply unless further additions to the order are requested. Other options include infeed and outfeed hoists and conveyors, tilt stations, operator platforms as well as walkways.