Content Attributes
A manufacturing technique that enables the mass production of components is injection molding. It operates by injecting molten materials into a mold (referred to as a “mold” in the US). Usually, it is employed as a mass manufacturing technique to create thousands of similar goods. Although the technique is most frequently employed with thermoplastic and thermosetting polymers. Injection molding may also be applied with metals, glassware, elastomers, and sweets.
How does it Function?
The creation of the mold in the injection molding machine is the first step in the injection molding process. The majority of molds are constructed of metal, often steel or aluminum. And carefully machined to fit the characteristics of the object they are to manufacture.
The material for the component is put into a heated barrel and combined using a helical-shaped screw after the mold maker has made the mold. Heating bands melt the material in the barrel, which is then fed into the cavity of the mold where it cools and hardens to take on the shape of the mold.
Using cooling lines that circulate water or oil from an external temperature controller helps shorten the cooling process. When the material has been set, plate molds (also known as “platens”) hold the molding tools open to allow the item to be removed using ejector pins.
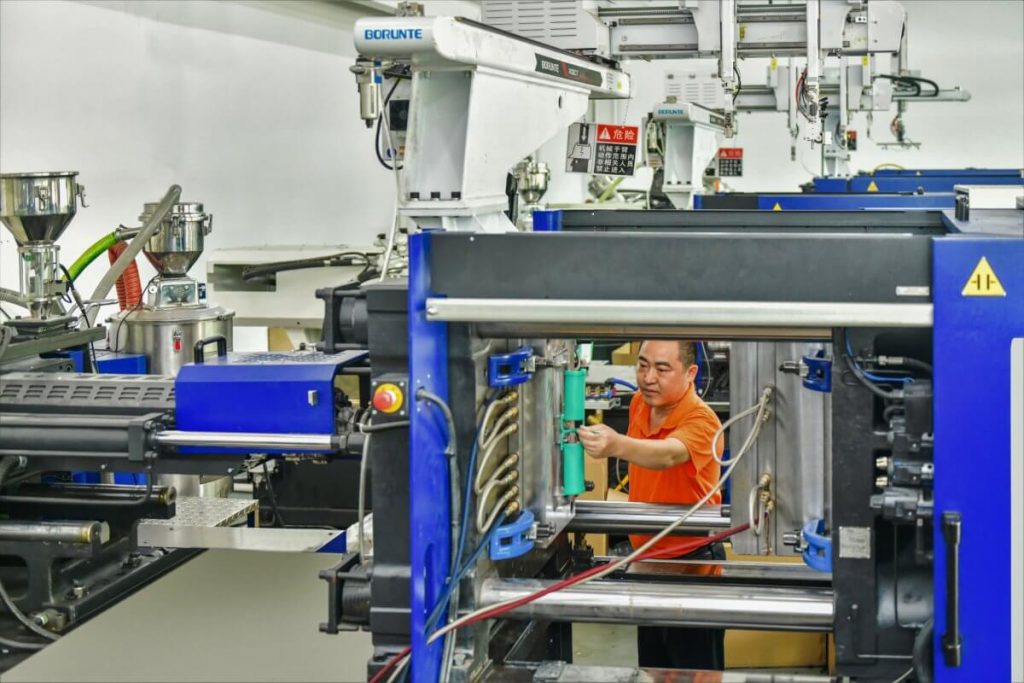
A two-shot mold is an injection molding technique that allows different materials to be blended into one object. This method may be used to give plastic products a plush feel, add color to a part, or create products with various performance qualities.
Molds might have a single cavity or several cavities. Multiple cavity molds can produce pieces with the same geometry or with distinct geometries in each cavity. Since aluminum has poor mechanical qualities and is vulnerable to wear, distortion, and damage from the injection and clamping pressures. It is not recommended for high-volume manufacturing or components with tight dimensional tolerances. Steel molds are more costly than aluminum molds while being more robust.
The form and features of the component, the materials used for the part and the mold, and the characteristics of the molding machine all need to be carefully designed for the injection molding process. As a result, while using injection molding, several factors need to be taken into account.
Uses for Injection Molding
A variety of frequently used goods, including ordinary plastic objects like bottle caps as well as remote control casings, syringes, and more, are made using the injection molding process. Additionally, it is frequently utilized in the production of bigger objects like automotive body panels.
When producing dozens or millions of identical pieces from a mold, injection molding is typically employed.
Advantages
The ability to scale up production to create a huge number of parts is injection molding’s major benefit. The price of production is quite inexpensive once the upfront costs of the design and the molds have been paid for. As more components are produced, production costs decrease.
Injection molding creates less waste than more conventional production techniques like CNC milling, which removes extra material. Even so, there is some waste produced by injection molding, primarily from the sprue, runners, gate positions, and any overflow material that spills out of the component cavity (also known as “flash”).
The third advantage of injection molding is that it enables the creation of multiple identical parts, which allows for part dependability and uniformity in high-volume production.
Disadvantages
While there are certain benefits to injection molding, there are also some drawbacks to the technique.
When it comes to tooling, injection molding might have expensive upfront expenses. A prototype part must be made before any pieces may be produced. A prototype mold tool has to be made and tested when this is finished. This whole procedure can be expensive and time- and money-consuming.
The production of big pieces in a single piece via injection molding is likewise not recommended. This is a result of the mold tools’ and injection mold machines’ size restrictions. Items that are too big to be produced by an injection molding machine must be produced in many sections and assembled afterward.
The last drawback is that significant undercuts might increase the cost of your project and require expert design to prevent it.
Applications
Numerous applications that call for a predictable production process employ injection molding. Toys, combs, musical instruments (and their parts), seats, tiny tables, storage containers, wire spools, packaging, bottle caps, mechanical parts, and automobile parts and components are among the manufactured goods that fall under this category.
The most popular method for producing plastic parts, especially in large quantities, is injection molding.
Injection-molded polymers that are often utilized include:
1. Acrylonitrile Butadiene Styrene (ABS) Industry uses this robust, impact-resistant material extensively. ABS has strong acid and basic resistance as well as low shrinkage rates and high dimensional stability.
2. Polycarbonate (PC) Polycarbonate is a sturdy, impact-resistant material with minimal shrinkage and exceptional dimensional stability. PC, transparent plastic with many optically clear grades available, may offer a high level of aesthetic quality and strong heat resistance.
Conclusion
There are several uses for injection molding in the industrial industry, especially for making large quantities of parts. The cost of production is modest after the tooling and molding are finished, even though they can be expensive. Injection molding is used to create components from a range of material types because it allows for the production of almost similar parts.